
Hot forging materials are available all over the world which has a positive impact on their final price. The excellent surface quality allows a wide range of finishing work as polishing, coating or painting, tailored to customers’ specific need. Also, as a technique hot forging is more flexible than cold forging, lots of customized parts can be manufactured in closed die forging. Hot closed die forged components possess increased ductility which makes them desirable for many shapes and applications. Closed die forging is the most common method of forging utilized in the industry to produce intricate and difficult geometries, offering countless possibilities for creating high strength components and tools with precision.īy comparision, closed die hot forging is the most widely used forging method. The high temperature during hot forging enables the highest possible level of material deformation and the access to complex 3D geometries. In warm forging the metal is heated to a range that is typically above room temperature, but below the re-crystallization temperature of the metal. In hot forging, the metal is heated to high temperatures then formed.

In cold forging the metal is not directly heated, but formed using high pressure. The closed die forging process can be done with cold forging, hot forging or warm forging. Often, closed die forging requires that the workpiece be moved through a series of impression cavities, at first forming the rough shape, then proceeding until a finisher cavity turns out the final product. A small amount of excess metal flows into a thin recess at the edges of the two dies called a flash gutter the flash cools quickly and then serves as a plug keeping the rest of the metal in the die.
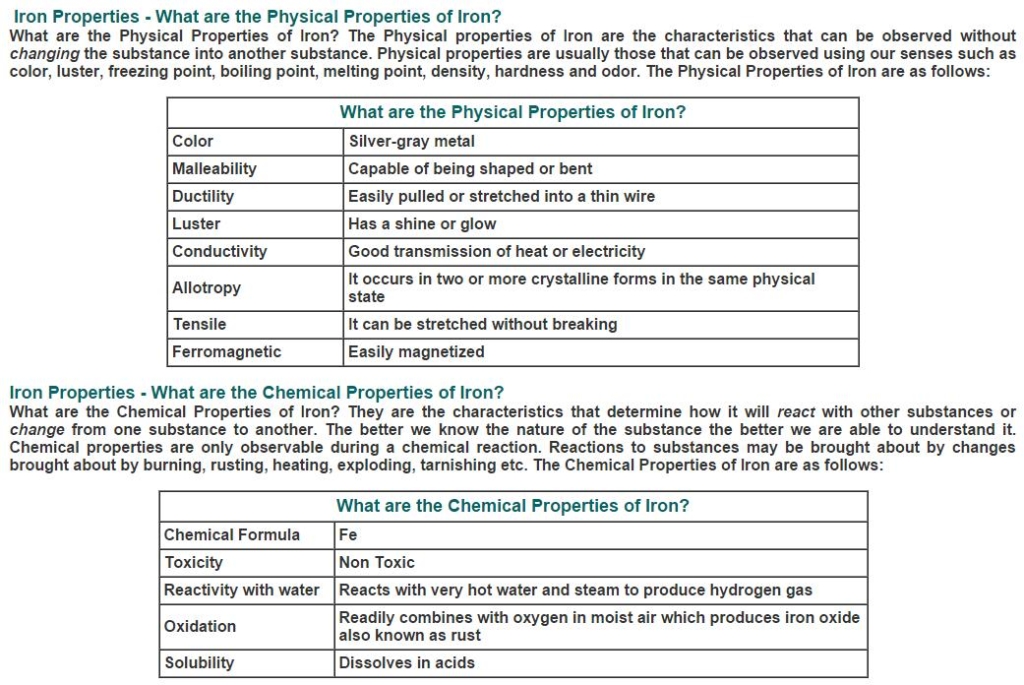
The moving die presses down onto the stationary die and the metal workpiece and causes the metal to flow into every part of the die and take its shape. Both dies contain an impression of the desired part shape. Closed die forging can produce a nearly limitless variety of 3-D shapes, and is capable of producing complex parts with tight tolerances.Ĭlosed die forging is operated under two tooling dies: a stationary die (anvil) and a moving die (hammer). In closed die forging, the hammer and anvil fully enclose the workpiece, forcing the metal to fill all areas of the dies.
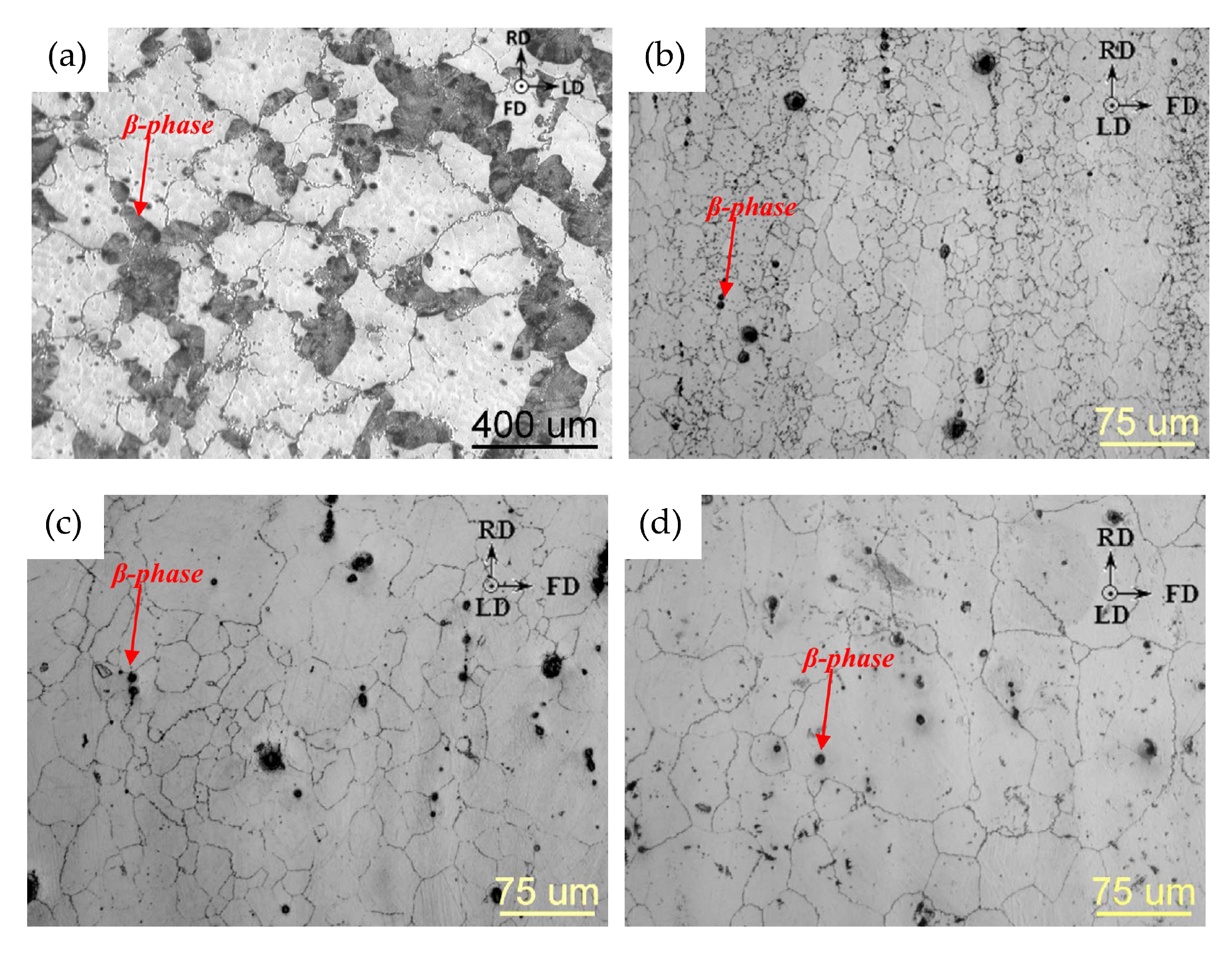
Closed die forging, one of the main forging process, involves the pressing or hammering of preformed metal blanks into a set of dies shaped as a three dimensional negative of the part to be produced.
